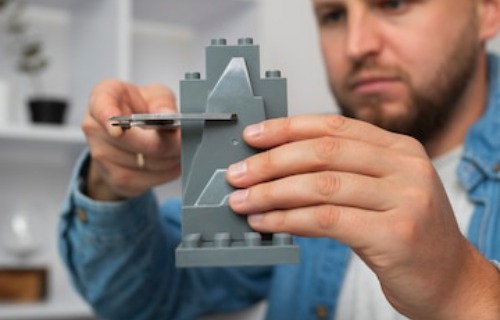
What is Post-Processing for 3D Printing?
Simply put, post-processing for 3D printing refers to any additional steps taken after a part is printed to improve its quality, durability, or aesthetics. Most 3D-printed parts require some level of post-processing before they are ready for use. This could involve removing support structures or excess material, washing and curing the part, sanding rough surfaces, or adding finishing touches like painting and coloring.
Think of it as the final step that transforms a raw 3D-printed piece into a polished, professional-looking product. Whether you're looking for a smoother surface, enhanced strength, or a customized look, our post-processing service plays a crucial role in achieving the desired results.
At 3D Specialist, we take post-processing for 3D printing to the next level by refining and perfecting every component to meet the highest standards of quality and aesthetics. Our comprehensive post-processing 3D printing services include sanding, painting, coating, and assembly, ensuring that each part is meticulously finished for optimal function and appearance. We focus on addressing imperfections and enhancing precision, so your 3D-printed and machined components achieve a professional-grade finish. With a commitment to excellence, our expert team tailors post-processing 3D printing solutions to align with your specific requirements, delivering results that enhance durability, performance, and visual appeal.
We provide professional post-processing to ensure that our customers receive the flawless parts
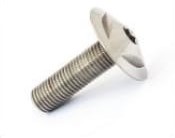
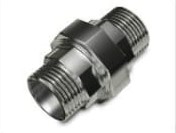
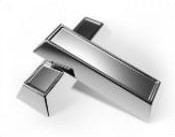
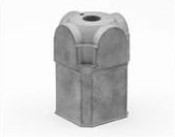
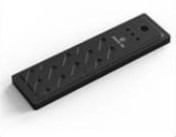
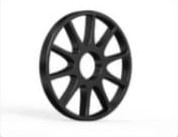
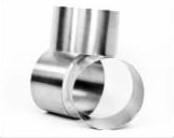
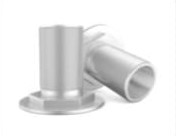
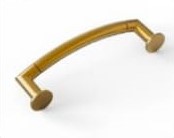
Threading
refers to the process of creating a helical structure, or thread, on the surface of a cylindrical object. This essential technique is widely used in manufacturing and engineering to enable parts to be screwed together securely.
Key Concepts
There are various threading standards, including Unified National (UN), Metric, and British Standard, each suited for different applications. Threads can be classified as internal (female) or external (male), and can vary in pitch, diameter, and angle.
Threading can be achieved through different methods such as cutting, rolling, or using taps and dies. Each method has its advantages depending on the material and the required precision.
Threading is crucial in applications ranging from fasteners and bolts to precision instruments and machinery. It allows for strong mechanical connections and precise adjustments.
Threads are created on various materials, including metals, plastics, and composites. Specialized tools like thread taps, dies, and thread mills are used to achieve the desired thread profile.
Understanding threading is fundamental for designing and assembling components that need to be joined or adjusted with high precision. Whether you're working on a simple project or complex machinery, mastering threading ensures reliability and performance in your designs.
Key Concepts
The primary goal of polishing is to remove imperfections, scratches, and oxidation from a surface, resulting in a smooth, shiny, and aesthetically pleasing finish. Polishing also helps in improving the surface's resistance to corrosion and wear.
Polishing can be done using various methods, including mechanical abrasion, chemical treatments, and manual polishing. Techniques vary based on the material being polished and the desired level of gloss.
- Mechanical Polishing: Involves using abrasive materials or tools, such as polishing wheels or pads, to mechanically grind down the surface. This method is common in metalworking and automotive refinishing.
- Chemical Polishing: Utilizes chemical solutions or compounds to dissolve surface imperfections and enhance the finish. This method is often used for delicate surfaces or materials that require a high level of precision.
- Manual Polishing: Involves hand tools and polishing compounds, allowing for greater control and finesse. This technique is frequently used in jewelry making and intricate crafts.
Polishing can be applied to a wide range of materials, including metals, plastics, glass, wood, and ceramics. Each material requires specific polishing compounds and techniques to achieve the best results.
The polished finish is crucial in numerous applications:
- Automotive: Enhancing the appearance of car exteriors and removing scratches.
- Jewelry: Achieving a brilliant shine on precious metals and gemstones.
- Metalworking: Providing a smooth finish to machined parts and components.
- Woodworking: Creating a sleek, smooth surface on furniture and cabinetry.
Proper polishing not only improves the visual appeal of a product but also enhances its durability and functionality. A well-polished surface is less prone to damage, easier to clean, and often more resistant to environmental factors.
Whether you're looking to perfect a piece of machinery, enhance the beauty of a handcrafted item, or achieve a showroom-quality finish, polishing is an essential process for achieving excellence in both function and appearance.
Polishing
Polishing is a process used to smooth and enhance the surface of a material, giving it a high-quality, reflective finish. This technique is essential in various industries, from manufacturing and automotive to jewelry and woodworking.
Sandblasting
Sandblasting, also known as abrasive blasting, is a technique used to clean, texture, or prepare surfaces by propelling abrasive materials at high speeds. This process is essential in various industries for its ability to remove contaminants, rust, and old coatings, as well as for creating specific surface textures.
Key Concepts
The main objectives of sandblasting are to clean surfaces, enhance adhesion for coatings, and create specific textures or finishes. It is particularly effective in removing stubborn contaminants, rust, and old paint from metal, stone, and other materials.
Sandblasting involves using compressed air to blast abrasive particles at a surface. The abrasives, which can range from sand and glass beads to aluminum oxide and steel grit, impact the surface and dislodge contaminants or create a rough texture.
- Types of Abrasives: Various materials are used depending on the desired outcome:
- Sand: Traditional abrasive, often used for general cleaning and surface preparation.
- Glass Beads: Used for a smoother finish and to clean without removing material.
- Aluminum Oxide: Effective for heavy-duty cleaning and surface profiling.
- Steel Grit: Ideal for industrial applications requiring robust abrasive action.
- Automotive: Removing rust and old paint from vehicle parts and bodies.
- Construction: Preparing surfaces for painting or coating, and cleaning stone and masonry.
- Manufacturing: Cleaning metal parts and preparing surfaces for further processing or coating.
- Art and Decoration: Creating intricate patterns and textures on glass, stone, and other materials.
- Efficiency: Quickly and effectively cleans large surfaces or complex geometries.
- Versatility: Adaptable to a wide range of materials and applications.
- Surface Preparation: Ensures better adhesion of paints and coatings by creating a roughened surface for improved bonding
Sandblasting not only improves the appearance of surfaces but also enhances their durability and prepares them for subsequent treatments. It is an essential process for achieving a clean, smooth, and properly prepared surface for various applications.
Key Concepts
- The primary goals of plating are to:
- Improve Aesthetics: Provide a decorative finish with a shiny or matte look.
- Enhance Durability: Increase resistance to wear, corrosion, and tarnishing.
- Reduce Friction: Apply materials that reduce friction and wear in mechanical parts.
- Conductivity: Improve electrical conductivity for electronic components.
- Various plating methods and materials are used depending on the desired properties and application:
- Electroplating: Uses electrical current to deposit metal ions from a solution onto the substrate. Commonly used metals include gold, silver, nickel, and chromium. Electroplating is popular for both decorative and functional purposes, such as in jewelry, automotive parts, and electronics.
- Electroless Plating: A chemical process that deposits metal onto a surface without the use of electrical current. This method is often used for coating complex shapes and providing a uniform finish. Nickel-phosphorus and copper are commonly used in electroless plating.
- Hot-Dip Plating: Involves immersing the substrate in a molten metal bath, such as zinc or aluminum. This method is widely used for coating steel to improve corrosion resistance, commonly seen in galvanized steel products.
- PVD (Physical Vapor Deposition): A vacuum process where metal vapor is deposited onto a substrate to form a thin, hard coating. PVD is used for applications requiring a high-performance, durable finish, such as in cutting tools and decorative finishes.
- Plating is utilized across various industries:
- Automotive: Enhancing the appearance and durability of parts such as bumpers, trim, and wheels.
- Electronics: Improving conductivity and protecting sensitive components, such as connectors and circuit boards.
- Jewelry: Providing a decorative finish with metals like gold and silver.
- Industrial: Coating tools and machinery to reduce friction and wear, extending their lifespan.
- Plating offers several benefits:
- Enhanced Appearance: Provides a bright, polished finish that can enhance the visual appeal of products.
- Improved Protection: Increases resistance to corrosion, wear, and abrasion.
- Cost-Effective: Allows for the use of less expensive materials while achieving the desired surface properties.
Plating not only adds aesthetic value but also improves the performance and longevity of components by providing essential protective and functional properties. Whether for decorative purposes or industrial applications, plating is a versatile process that delivers significant benefits in both appearance and functionality.
Plating
Plating is a surface finishing process where a thin layer of metal is applied to a substrate to enhance its appearance, durability, and resistance to corrosion. This technique is widely used in manufacturing and decorative applications to improve the functionality and visual appeal of various products.
Coloring
Coloring is the process of applying color to materials to enhance their appearance, create visual appeal, or meet specific design requirements. This technique is widely used in various industries, from manufacturing and textiles to art and design, to add aesthetic value and distinguish products.
Key Concepts
- Coloring serves several important functions:
- Aesthetic Enhancement: Adds visual appeal and can significantly impact the look and feel of a product.
- Identification and Branding: Helps in distinguishing products, supporting brand identity, and providing color-coded information.
- Functional Benefits: Certain coloring methods can also provide protective qualities, such as UV resistance or enhanced visibility.
- Different techniques are used depending on the material and desired outcome:
- Painting: Involves applying liquid paint to a surface using brushes, rollers, or spray guns. Painting is commonly used in automotive, industrial, and architectural applications to achieve both decorative and protective finishes.
- Anodizing: An electrolytic process used to enhance the natural oxide layer on metals, such as aluminum. Anodizing can be done with dyes to create a range of colors while increasing corrosion resistance and surface hardness.
- Coating: Involves applying a colored layer of material, such as a powder coating or electroplated finish, to a surface. This method provides a durable, uniform color and often includes additional protective properties.
- Manufacturing: Adding color to plastics, metals, and other materials for both functional and decorative purposes.
- Art and Design: Creating visual artwork and custom designs using various coloring techniques.
- Consumer Goods: Enhancing the appearance of products like electronics, furniture, and household items.
- Visual Appeal: Enhances the attractiveness and marketability of products.
- Customization:Allows for personalized designs and unique color choices.
- Functional Properties: Provides additional features such as UV protection or improved visibility.
Coloring not only beautifies products but also adds value by enabling customization, improving functionality, and supporting brand identity. Whether for practical use or artistic expression, coloring is a key element in product design and development.
Key Concepts
- The primary goals of heat treatment include:
- Strengthening: Improving the hardness and tensile strength of materials to handle greater loads.
- Toughening: Enhancing the material’s ability to withstand impact and reduce brittleness.
- Stress Relief: Reducing internal stresses caused by previous manufacturing processes to prevent warping or cracking.
- Softening: Increasing ductility to make materials easier to machine or shape.
- Several heat treatment methods are used depending on the material and desired properties:
- Annealing: Involves heating a material to a specific temperature and then slowly cooling it. Annealing softens the material, reduces internal stresses, and improves ductility. It is commonly used for metals like steel and aluminum.
- Quenching: Rapidly cooling a material, usually by immersion in water or oil, after heating to a high temperature. This process increases the hardness and strength of the material but can also make it more brittle. Quenching is frequently used in the hardening of steel.
- Tempering: Performed after quenching to reduce brittleness and increase toughness. The material is reheated to a lower temperature and then cooled, which balances hardness and ductility.
- Normalizing: Heating a material to a temperature above its critical point and then air cooling it. This process refines the grain structure, improves mechanical properties, and eliminates internal stresses, resulting in a more uniform material.
- Case Hardening: A process that hardens the surface of a material while leaving the core softer. Techniques such as carburizing and nitriding are used to improve wear resistance and fatigue life of components.
- Solution Treatment: Heating an alloy to dissolve soluble phases and then rapidly cooling it to lock the desired structure in place. This process is common in the treatment of aluminum and titanium alloys.
- Aging: Heating or holding a material at a specific temperature for an extended period to increase hardness and strength through the formation of precipitates. Aging is often used in aluminum alloys.
- Heat treatment is essential in various industries:
- Automotive: Enhancing the performance and durability of engine components, gears, and springs.
- Aerospace: Strengthening materials used in aircraft and spacecraft to withstand extreme conditions.
- Construction: Improving the properties of structural steels and reinforcing bars.
- Manufacturing: Processing tools, dies, and machinery parts to achieve optimal hardness and toughness.
- Heat treatment offers several benefits:
- Improved Mechanical Properties:Increases strength, hardness, and toughness as needed for specific applications.
- Enhanced Durability: Provides resistance to wear, fatigue, and corrosion.
- Precision and Control: Allows for exact modifications to material properties, ensuring performance meets required specifications.
Heat treatment is a fundamental process in material science and engineering that enables the optimization of material properties for enhanced performance and reliability. Whether for industrial components or high-performance applications, heat treatment is crucial for achieving the desired characteristics in various materials.
Heat treatment
Heat treatment is a critical process used to alter the physical and chemical properties of materials, primarily metals and alloys, to achieve desired mechanical characteristics. This process involves heating and cooling materials in a controlled manner to enhance their strength, hardness, ductility, and overall performance.
Laser etching
Laser etching is a high-precision marking and engraving process that utilizes laser technology to create detailed and permanent designs on various materials. This advanced technique is widely used in industries ranging from manufacturing and electronics to art and customization, offering unparalleled accuracy and versatility.
Key Concepts
- Laser etching is employed to achieve several objectives:
- Marking: Creating clear, readable text, logos, or codes for identification and traceability.
- Engraving: Producing intricate designs and patterns on surfaces for decorative or functional purposes.
- Customization: Personalizing products with unique designs or messages, making items one-of-a-kind.
- The laser etching process involves directing a focused laser beam onto the material's surface. The laser’s intense energy removes or alters the material, producing precise markings or engravings. The process typically includes:
- Preparation: Setting up the design file and selecting the appropriate parameters for the laser etching machine.
- Laser Operation: The laser beam scans the surface, etching the design according to the specifications.
- Finishing: Depending on the material and application, additional finishing steps may be applied to enhance the appearance or functionality.
- Metals: Steel, aluminum, and stainless steel are commonly etched for industrial parts, tools, and decorative items.
- Plastics: Used for marking and branding on plastic components and consumer goods.
- Glass: Produces elegant and permanent designs for trophies, awards, and custom glassware.
- Wood: Creates detailed engravings for art, signage, and personalized gifts.
- Leather: Adds unique designs or text to leather goods such as wallets, belts, and bags.
- Manufacturing: Marking parts and tools with serial numbers, barcodes, and logos for traceability and quality control.
- Electronics: Etching circuit boards and components for identification and functionality.
- Personalization: Customizing products like jewelry, awards, and promotional items with names, dates, or designs.
- Art and Design: Creating intricate patterns and artwork on various surfaces, including wood and glass.
- High Precision:Achieves intricate details and fine lines with exceptional accuracy.
- Permanent Marking: Produces durable and resistant marks that do not wear off easily.
- Non-Contact Process:Minimizes material distortion and reduces wear on tools compared to traditional engraving methods.
- Versatility: Capable of working with a wide range of materials and achieving various design effects.
Laser etching combines cutting-edge technology with precise craftsmanship, providing a reliable solution for marking, engraving, and customizing materials. Whether for industrial applications, personal items, or artistic creations, laser etching delivers high-quality, lasting results with unmatched detail and versatility.
Key Concepts
- The anodizing process is designed to achieve several objectives:
- Corrosion Resistance: Increases the metal's resistance to environmental factors such as moisture and chemicals.
- Durability: Enhances surface hardness and wear resistance, extending the lifespan of components.
- Aesthetic Appeal: Provides a range of color options and a consistent, attractive finish.
- Surface Adhesion: Improves the adhesion of paints and coatings for enhanced finishing options.
- Anodizing involves immersing the metal part in an electrolytic solution and applying an electrical current. The process includes:
- Cleaning: Preparing the metal surface by removing contaminants and oxides.
- Electrolytic Bath: Submerging the metal in an acid electrolyte, such as sulfuric or oxalic acid.
- Current Application: Passing an electrical current through the electrolyte, causing oxygen to combine with the metal surface to form a thicker and more durable oxide layer.
- Coloring (Optional): Adding dyes or pigments to the anodized layer to achieve various colors and finishes.
- Case Hardening: A process that hardens the surface of a material while leaving the core softer. Techniques such as carburizing and nitriding are used to improve wear resistance and fatigue life of components.
- Sealing: Treating the anodized surface to close the pores and enhance corrosion resistance.
While aluminum is the most commonly anodized metal, anodizing can also be applied to other metals such as titanium, magnesium, and zinc. Each metal requires specific anodizing conditions to achieve the desired results.
- Anodizing is used across a variety of industries for both functional and decorative purposes:
- Aerospace: Protecting components from harsh environmental conditions and improving structural integrity.
- Automotive: Enhancing the appearance and durability of parts such as trim, wheels, and engine components.
- Construction: Providing a decorative and protective finish for architectural elements like window frames and facades.
- Consumer Goods: Adding aesthetic appeal to products such as electronics, cookware, and sports equipment.
- Anodizing offers several significant benefits:
- Enhanced Corrosion Resistance:Provides superior protection against oxidation and environmental damage.
- Increased Hardness: Strengthens the surface, making it more resistant to scratches and wear.
- Color Options: Allows for a wide range of colors and finishes to meet design preferences.
- Environmentally Friendly: Anodizing is a relatively eco-friendly process, producing no hazardous by-products.
Anodizing is a valuable process for improving the performance and appearance of metal components. By increasing corrosion resistance, durability, and aesthetic flexibility, anodizing delivers both practical and visual advantages, making it an essential technique in various industrial and consumer applications.
Anodizing
Anodizing is an electrochemical process that enhances the natural oxide layer on metal surfaces, primarily aluminum, to improve their durability, appearance, and resistance to corrosion. This widely used technique creates a protective coating that is integral to the metal, offering both functional and aesthetic benefits.
Our Services
Explore our website to learn more about our comprehensive suite of services and cutting-edge capabilities. Join us on the journey to revolutionize manufacturing and unlock new possibilities for your business with Advance Manufacturing Solutions.