At 3D Specialist we specialize in providing advanced collaborative robots
Our collaborative robots are designed to work seamlessly alongside human operators, enhancing productivity and safety in diverse industrial settings. We offer a range of cobots that can handle repetitive tasks such as assembly, packaging, and machine tending with precision and reliability.
Our team excels in system integration, ensuring that each cobot is expertly integrated into your existing workflows and production lines. We provide end-to-end solutions that include the initial consultation, customized setup, and ongoing support. From designing tailored automation solutions to programming and fine-tuning, our goal is to ensure that the cobots operate efficiently and effectively, minimizing downtime and maximizing your return on investment.
By choosing our cobots and system integration services, you benefit from increased operational efficiency, reduced labor costs, and enhanced safety for your workforce. Our expertise in integrating advanced robotics with your current systems allows for a smooth transition and immediate gains in productivity. Whether you’re looking to streamline production processes or innovate your manufacturing operations, we are here to help you achieve your automation goals with state-of-the-art collaborative robots and expert integration services.
What can we use the Collaborative Robots for?
Collaborative robots, or cobots, are versatile and increasingly popular in various industries due to their ability to work alongside human operators safely and efficiently. Here are some key applications:
Manufacturing and Assembly
Cobots handle repetitive tasks like assembly, material handling, and quality inspection, improving efficiency and consistency while freeing human workers for more complex tasks.
Packaging
In packaging operations, cobots automate tasks such as sorting, packing, and palletizing products, enhancing speed and accuracy while reducing labor costs.
Machine Tending
Cobots can manage machine tools, loading and unloading materials or finished products, thus reducing downtime and increasing production rates.
Lab Automation
In laboratories, cobots assist with tasks such as sample handling, pipetting, and data collection, ensuring precise and reproducible results while allowing researchers to focus on analysis and experimentation
Healthcare and Medical
Cobots support tasks like surgical assistance, rehabilitation, and patient handling. They help in repetitive tasks like dispensing medication or performing routine diagnostics, increasing efficiency and reducing human error.
Electronics and Precision Assembly
Cobots perform delicate and precise tasks such as soldering, component placement, and inspection, which are critical for electronics and high-precision industries.
Education and Training
In educational settings, cobots serve as hands-on tools for teaching robotics, programming, and automation concepts, providing students with practical experience.
Retail and Customer Service
Cobots assist with stocking shelves, managing inventory, and even interacting with customers, enhancing service efficiency and customer satisfaction
Agriculture
Cobots help with tasks such as planting, harvesting, and packaging crops, improving productivity and reducing the physical strain on human workers
Logistics and Warehousing
Cobots manage tasks like sorting, picking, and transporting goods within warehouses, streamlining operations and enhancing order fulfillment processes
5 key differences between collaborative robots and robots
Traditional industrial robots provide full automation of assembly lines and can work entirely without human assistance. They also often carry bulky equipment, such as large welding tools, while performing their functions with speed and high dexterity. As a result, employees can take on other tasks that require problem solving or specific work, reducing the chance of repetitive motion injuries.
Meanwhile, a cobot typically assists a human operator. It can perform some of the dangerous, tiring, and tedious tasks that an employee would otherwise have to do alone. It may also involve more complex tasks that cannot be fully automated, such as handling wiring inside equipment. This teamwork between humans and cobots results in a more efficient workplace that does not come at the expense of factory work.
Cobots may still outperform cobots in terms of speed, but they are designed with production output in mind, not human safety. Even if they come into contact with an employee and cause harm, the robot will only stop when it receives an
appropriate command. To prevent workers from accidentally getting caught in moving parts, these robots are placed behind fences or cages.
Human safety is a major concern in the design of cobots, which have built-in safety mechanisms that meet established safety requirements for human collaboration. If a cobot detects a human nearby, it may move more slowly, or stop if the human is close enough. If something gets in its way during an operation, it stops immediately and waits for a command. As a result, cobots may not even need a safety cage, although this ultimately depends on a formal risk assessment based on their designated functions.
Another difference between robots and cobots is the skills required for programming. To give instructions to a robot, an
employee must have advanced computer coding skills. Also, most robot manufacturers have their own programming language
that employees must learn to get anything done. While learning BASIC/Pascal makes most of these languages easier to use, the sheer number of individual languages has been a problem for assembly lines that use numerous machines from different manufacturers.
On the other hand, an employee giving instructions to a cobot may not need any stock coding knowledge at all. Cobots,
such as the collaborative robot series, offer a simple, easy-to-use interface that doesn’t require any coding. More machines are even able to share the information they gain with other cobots. In the future, they may just have to learn new functions by watching an operator.
This also means that cobots will be easier to reprogram in the future. A single cobot can be reprogrammed and redeployed
as many times as the production chain needs.
Robots are usually bolted to the floor. Once they are operational, they usually do not need to be moved around the factory. This can also be considered a safety need, keeping the robot in place regardless of the speed and power required for its task.
Cobots are usually light enough for a single worker to carry. Employees can also move them easily using a mobile base.
Most cobots can also be mounted on a wall or ceiling. There are also a variety of end effectors available, including grippers and drills, which increase the flexibility of cobots.
Due to their speed and full automation, robots are still best for tasks with high quotas or hazardous environments (such as
exposure to lead or heat). Cobots can also work without assistance, but they are still ideal for jobs that require the cooperation of a human operator. They are useful for small and medium-sized enterprises, helping these companies take a step towards automation and improve their competitiveness. This does not mean that cobots do not have a place in large factories, where they can fill the skills gap between humans and industrial robots.
Robots may be better for handling heavier operations, but cobots are easier to set up, more flexible, and better suited for jobs that require high precision. Neither is necessarily better than the other by default, as it can still depend on the needs of the assembly line. But in the case of cobots, they are undoubtedly ideal for businesses that still prefer human supervision but need to improve production efficiency.
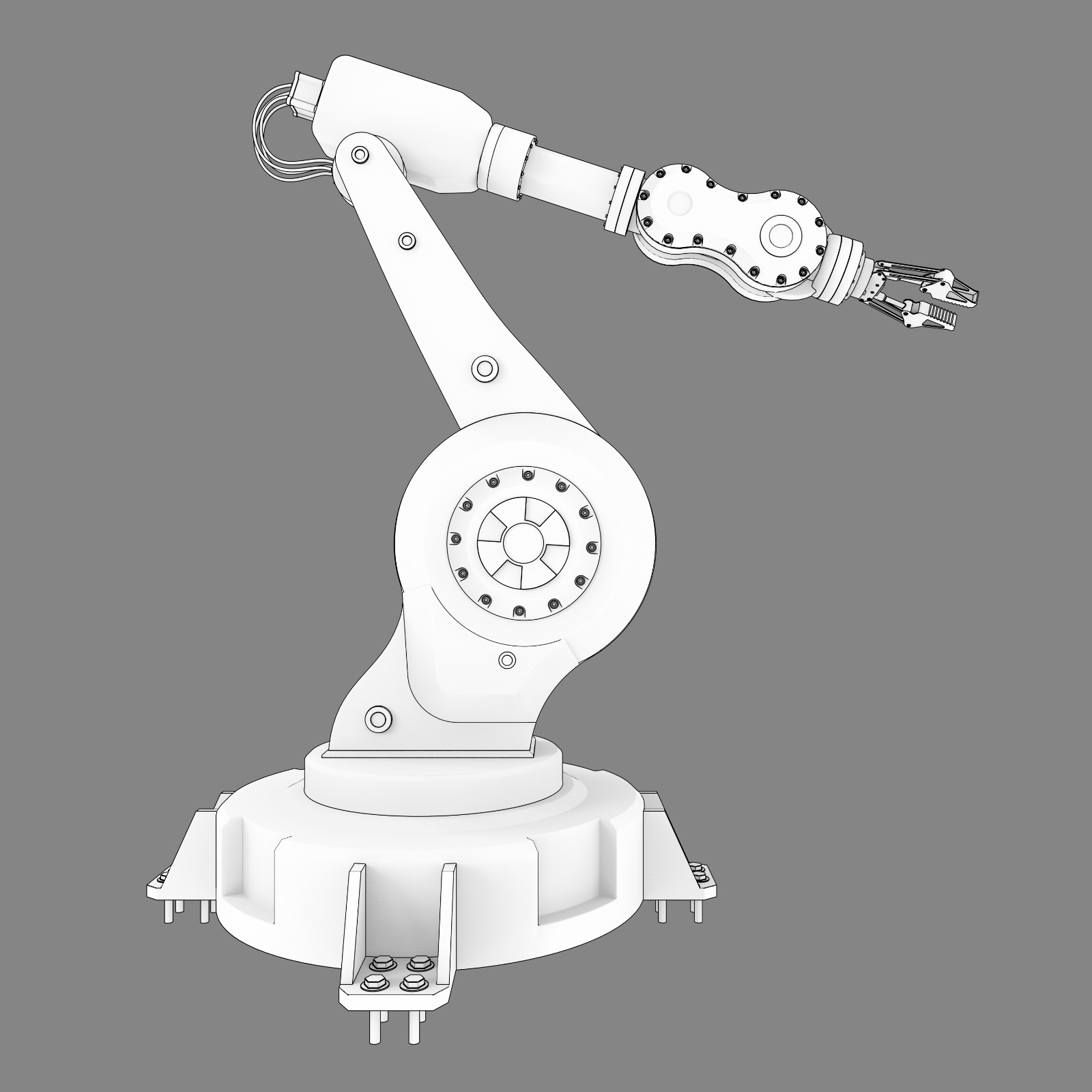
If you’re looking to integrate collaborative robots into your workflow, our team is here to help you every step of the way. Our experts work closely with you to understand your specific needs and operational goals, ensuring that we design and implement a solution that seamlessly fits into your existing processes.
From initial consultation and customized cobot selection to detailed system integration and ongoing support, we provide a comprehensive service tailored to enhance your productivity and efficiency.
By choosing us, you gain access to cutting-edge technology and expert guidance, making the transition to a more automated and streamlined operation smooth and effective.
Reach out to us today to explore how our collaborative robots can transform your workflow and drive your business forward.
Get A QuoteOur Services
Explore our website to learn more about our comprehensive suite of services and cutting-edge capabilities. Join us on the journey to revolutionize manufacturing and unlock new possibilities for your business with Advance Manufacturing Solutions.